Carbon Fiber
Mitsubishi Chemical Carbon Fiber and Composites offers one of the most diverse carbon fiber product ranges on the market today. Our carbon fibers are available in filament counts ranging from 2K to 60K, in both PAN-based and Pitch-based technologies. Carbon fibers are stronger than steel and lighter than aluminum enabling the light-weighting of structural applications.
Our standard modulus carbon fibers are manufactured in both Sacramento, California and Evanston, Wyoming. Carbon fibers are ideal for applications ranging from aircraft structure, pressure vessels, wind blades, and various sporting goods products.
In addition we offer an extensive range of Pyrofil and DIALEAD intermediate and high modulus products. These products are manufactured in Otake, Toyohashi, and Sakaide Japan.
Grafil, Pyrofil and DIALEAD carbon fibers are available for shipment from our Sacramento, California facility.
Fiber Type
Carbon Fiber
Find Which Fiber is Right For You
Vertical Integration
Our participation throughout the carbon fiber composites value chain uniquely positions Mitsubishi Chemical Carbon Fiber and Composites, Inc. to fully understand every step of the processes used to produce carbon fiber; both PAN and PITCH based carbon fibers.
For PAN based carbon fibers, our proprietary carbon fiber process begins in a world scale synthetic fibers plant and concludes in highly sophisticated carbonization facilities in the US and Japan. We start by combining commodity raw materials in a series of chemical reactions to produce acrylonitrile (AN), which is then polymerized to form polyacrylonitrile (PAN). This PAN material is then spun into a high quality precursor, which is a critical step to ensures the maximum potential properties and consistency of the carbon fiber. This potential is realized during the carbonization process; a precisely controlled pyrolysis of the PAN precursor used to produce the widest range of PAN based carbon fiber products available to the industry.
For our pitch-based carbon fiber, DIALEAD; the production processes employed by Mitsubishi Chemical are supported by many years of developing proprietary technologies. Our DIALEAD carbon fiber has a high carbon content ratio, thereby maintaining the chemical stability of composite materials. Our precise manufacturing process is utilized to structure graphite plates in a highly oriented vertical direction. This results in unique features such as lightweight, high stiffness, high thermal conductivity, and ultra low thermal expansion coefficient.
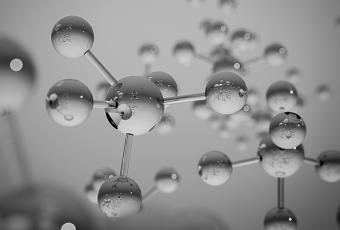
01
Monomers
Basic raw materials consisting of simple molecular structures (monomers) are combined to produce Acrylonitrile (AN). AN is then polymerized to form polyacrylonitrile (PAN). Mitsubishi Rayon uses the highest grade materials available to create AN and PAN.
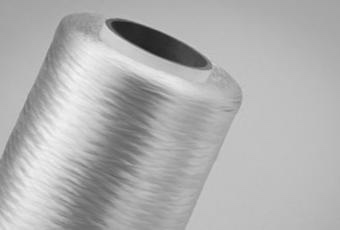
02
Precursor
A solution of PAN is then spun into precursor. The process of creating precursor heavily influences the quality and consistency of the carbon fiber. It is a process in which Mitsubishi Rayon has refined and perfected over the past 80-years.
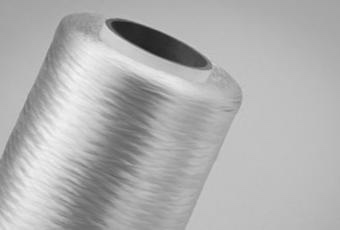
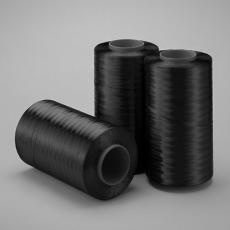
03
Carbon Fiber
Precursor is oxidized and carbonized in ovens to produce carbon fiber. Mitsubishi Rayon produces carbon fiber for a variety of different applications and is one of the largest manufacturers of carbon fiber in the world.
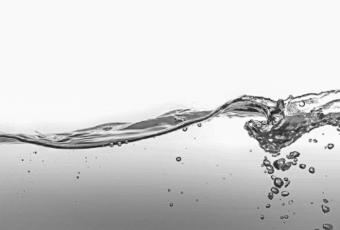
04
Resins
Precursor is oxidized and carbonized in ovens to produce carbon fiber. Mitsubishi Rayon produces carbon fiber for a variety of different applications and is one of the largest manufacturers of carbon fiber in the world.
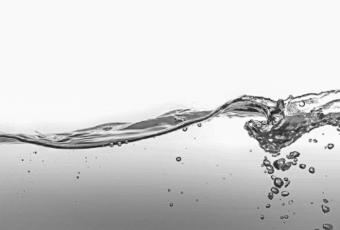
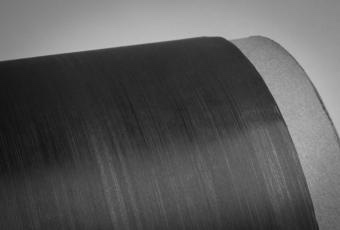
05
Prepeg
Carbon fibers are impregnated with resin to produce ready-to-mold material in sheet form. Mitsubishi Rayon produces a variety of different types of prepreg for many different applications (e.g. aerospace, sporting goods, etc.).
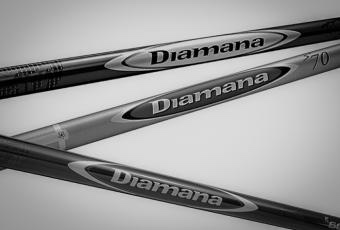
06
Golf Shafts
Different types of prepreg are then cut into specific patterns and rolled to create a composite golf shaft. Mitsubishi Rayon has over 20-years of experience in designing and developing premium, performance oriented golf shafts.
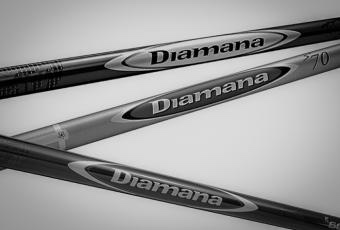